40+ Years of Expertise in Complex Projects for Diverse Industry Sectors
Our Expertise
Life Sciences
Elevating Life Sciences through Precision Construction
In the field of life sciences, Sun Construction brings its expertise as a general contractor to create specialized facilities that enable groundbreaking research, pharmaceutical production, medical device manufacturing, and more. With our commitment to excellence, our dedicated team works closely with clients in the life sciences industry to bring their visions to life, providing innovative solutions that meet their unique requirements.
Our vision at Sun Construction is to contribute to the advancement of the life sciences industry by providing cutting-edge construction services. As a trusted general contractor, we understand the importance of creating state-of-the-art facilities that enable breakthrough research, innovation, and the development of life-saving treatments. Through our expertise and dedication, we aim to shape a better future for the life sciences community and society as a whole.
Advanced Manufacturing
Innovate, Fabricate, Elevate: Pioneering Excellence in Advanced Manufacturing
In the field of advanced manufacturing, at Sun Construction we bring our expertise in construction to create state-of-the-art facilities that integrate automation, lean principles, and sustainable practices. Our dedicated team works closely with manufacturing companies to understand their specific needs, processes, and goals, ensuring that our construction solutions align with their vision and enable them to stay at the forefront of their industry.
We execute our work with industry-leading effectiveness and consistency. We understand that the advanced manufacturing sector demands precision, efficiency, and adaptability. With meticulous attention to detail and a focus on quality, we deliver construction solutions that meet the highest standards, enabling our clients to optimize their manufacturing processes and achieve operational excellence.
Open Advanced Manufacturing Portfolio
Government
Excellence in Government Construction: Delivering on Time, Within Budget, and Beyond Expectations
In the government sector, we bring our expertise in construction to projects that span various domains such as public infrastructure, civic buildings, educational institutions, and healthcare facilities. Our experienced team works closely with government organizations to understand their unique objectives, regulatory compliance, and community impact, ensuring that our construction solutions align with their vision and purpose.
We execute our work with industry-leading effectiveness and consistency, setting the bar for excellence in the construction industry. We understand the importance of delivering government projects on time, within budget, and to the highest quality standards. Our attention to detail, meticulous planning, and skilled workforce ensure that our construction solutions meet and exceed expectations, creating lasting value for government organizations and the communities they serve.
Open Government Portfolio
High-Tech
Building High-Tech Futures: Precision, Reliability, Excellence
We are committed to executing our work with industry-leading effectiveness and consistency. We understand that the high-tech sector demands precision, reliability, and state-of-the-art infrastructure. With meticulous attention to detail, we deliver construction solutions that meet the highest standards of quality, functionality, and sustainability. Our pursuit of excellence sets us apart and ensures that our clients’ visions are brought to life with exceptional results.
In the high-tech sector, we bring our expertise in construction to create state-of-the-art facilities that accommodate advanced research and development, data centers, manufacturing plants, and more. Our dedicated team works closely with high-tech companies to understand their specific needs and challenges, ensuring that our construction solutions align with their business objectives. Additionally, Sun is particularly adept at working within occupied and operational facilities where integration of systems is essential while maintaining our client’s ability to conduct business as usual.
Open High-Tech Portfolio
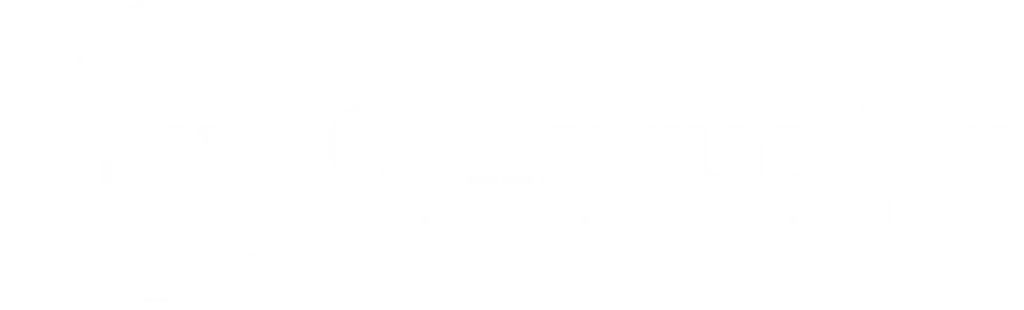
Adaptable By Design
Special Projects Division
At Sun Construction, we understand that not all projects are created equal. That’s why our Special Projects Division provides tailored solutions for smaller-scale projects across a range of industries including the life sciences, technology, manufacturing, and government sectors.
Our team of specialized experts is uniquely qualified to meet the specialized requirements and skill sets crucial to the construction and renovation of clean rooms, cGMP facilities, secure environments, and other critical built environments within these industry sectors.
What sets us apart is our commitment to delivering excellence in every project we undertake. Whether it’s designing a cutting-edge clean room facility for a pharmaceutical company or renovating a secure environment for a government agency, we take pride in our workmanship and pay close attention to detail in every aspect of every project, no matter the size. From planning and design to execution and completion, we ensure that every project is carried out with precision.
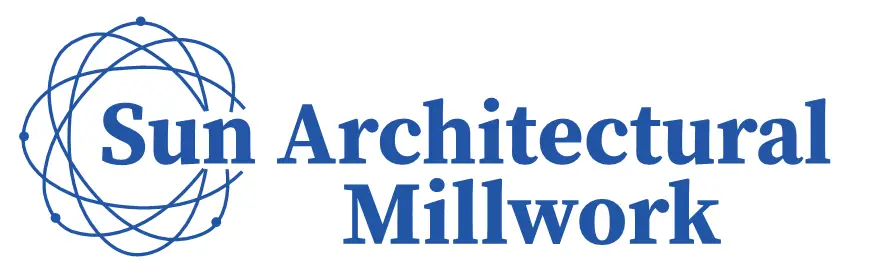
Sun Architectural Millwork
Excellence in Government Construction: Delivering on Time, Within Budget, and Beyond Expectations
Specializing in reclaimed materials, traditional wood, plastic laminate, European-style cabinets, and more, we are your one-stop destination for exceptional custom cabinetry and millwork.
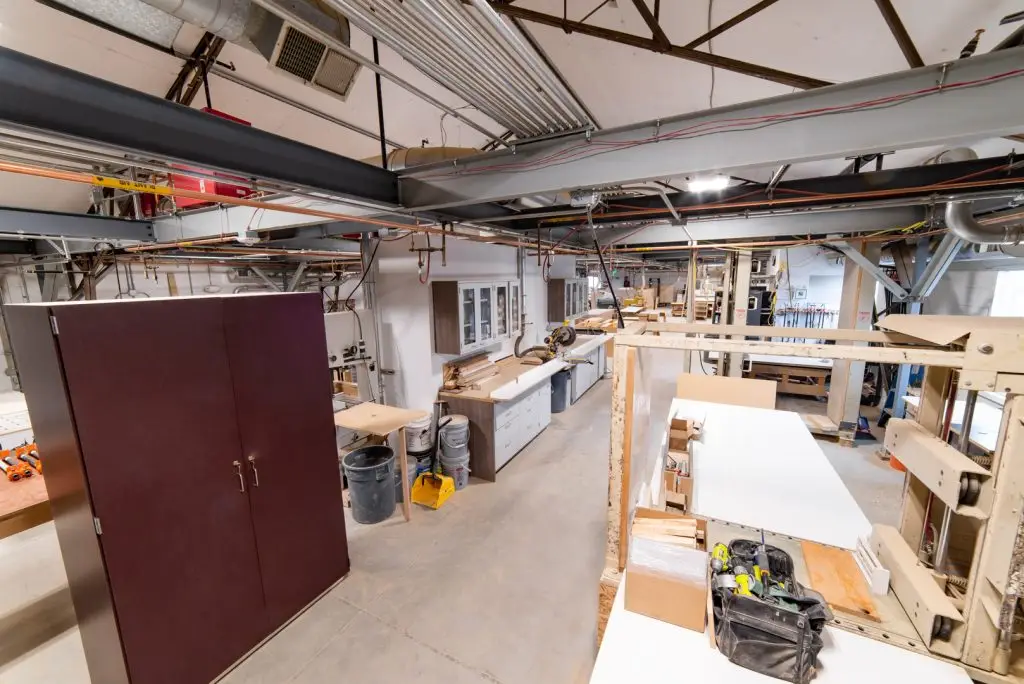